This paper will hopefully help in the selection of an appropriate polymer for your application. The first thing to keep in mind is: that polymer selection is dictated by the required performance. Due to the continual increase in polymer demand, the performance of polymers has been heavily modified to conform to various customer-driven needs. Thankfully we now have many polymer options to choose from, but now with all the options picking the appropriate plastic can be a challenge. Within this paper we will show how using simple logical decisions, a designer can select the most appropriate polymer for the job.
Plastics can be divided into two major categories: thermoplastic and thermoset. Thermoplastic polymers are formed by applying heat and can be reformed multiple times. Thermoset polymers are formed chemically, by radiation or heat and are irreversible. The focus of this paper will be directed toward thermoplastics. The table below demonstrates a sample of thermoplastic choices available on the market.
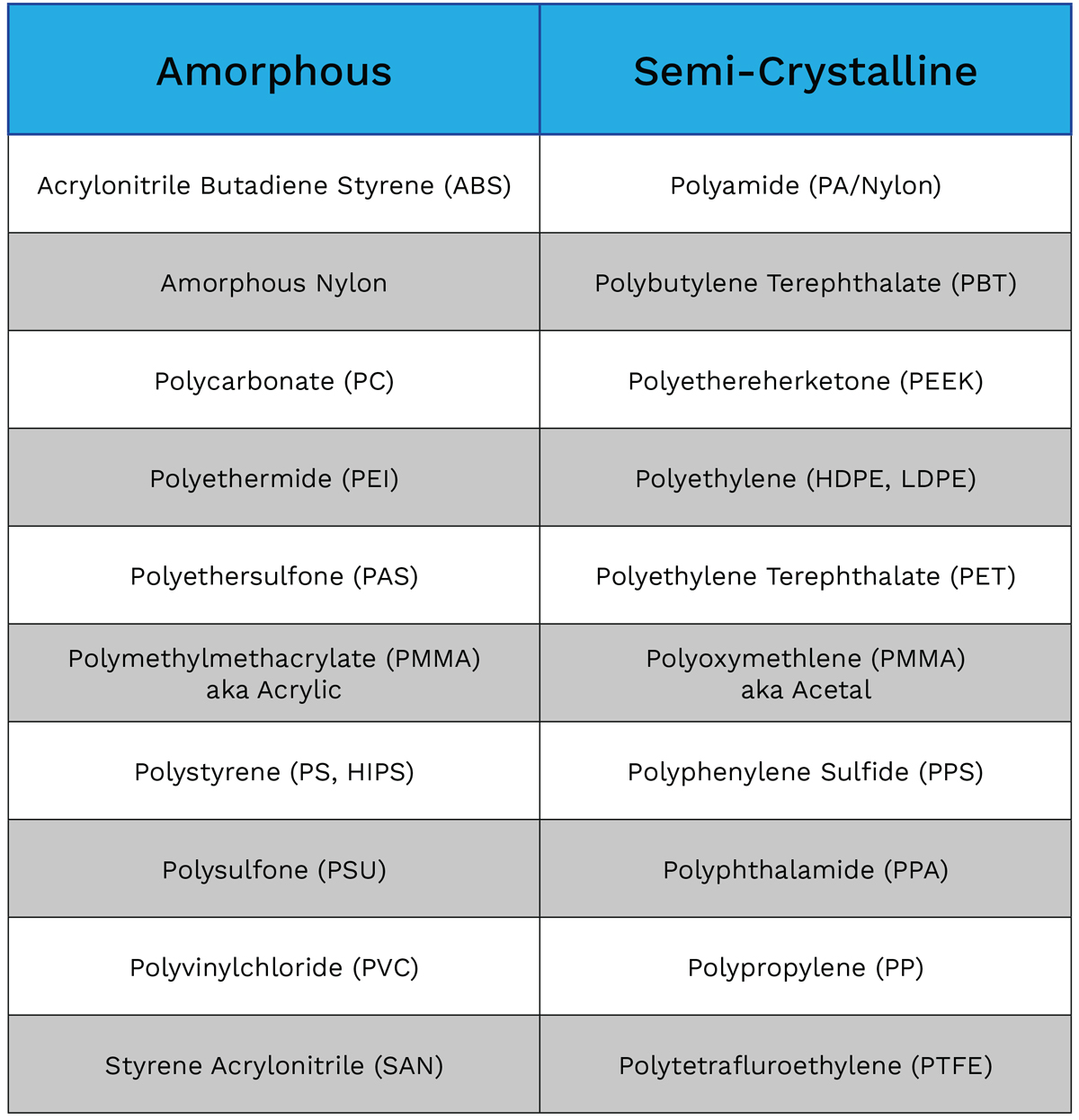
Polymer pellets can be blended together physically to create desired performance characteristics. Single-phase blending is where both components are soluble in each other like salt and water.
Multi-phase blending is where mixing occurs but maintains distinct area’s in the mixture. The polymer can also be modified by including rubber like additives to increase the impact resistance and glass like additives to increase the rigidity. Polymers can also be combined together chemically in a process called copolymerization. Copolymerization is where two homopolymer chains are chemically bonded.
Thermoplastic polymers are separated further into two main categories: semi-crystalline and amorphous. As the table above represents, there is approximately a 50/50 split of amorphous and semi-crystalline polymers to choose from throughout the industry. Semi-crystalline plastics, at a monomer chain level, create ordered sections that pack tightly together. Amorphous is without ordered sections and does not pack as tightly together. The packing difference leads to a variety of unique characteristics, morphology, that help narrow a designer's selection.
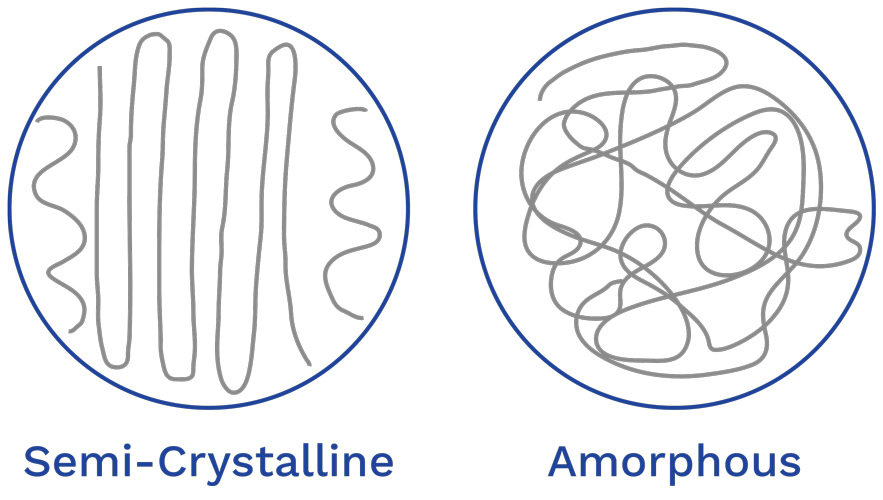
Amorphous polymers have less shrinkage and warpage as compared to the semi-crystalline. Semi-crystalline material has a higher shrink and greater warpage due to monomer chains packing tightly together to form crystalline regions, more crystalline regions results in greater shrinkage. Semi-crystalline has higher energy regions due to the crystalline packing and therefore has a higher chemical/abrasion resistance. Amorphous polymers can be used in a transparent optical application because monomer chains are not as tightly packed and therefore allow light to pass through. Semi-crystalline is packed tightly and will reflect light off within the crystalline regions. For processing, the amorphous has a wide temperature range that the material will flow and semi-crystalline has a sharp. Semi-crystalline polymers are able to flow better into small/thin-wall sections.
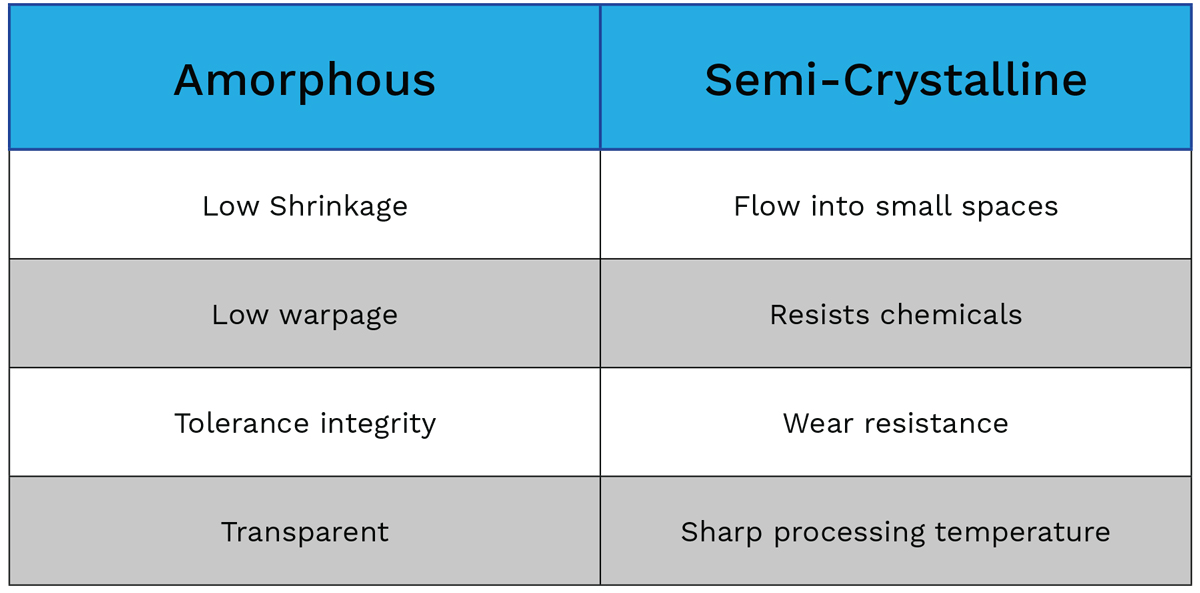
Amorphous and semi-crystalline polymers are typically classified in three categories: commodity, engineering and specialty. Viewing polymers from commodity to engineering the thermal performance increases, but the cost also increases.
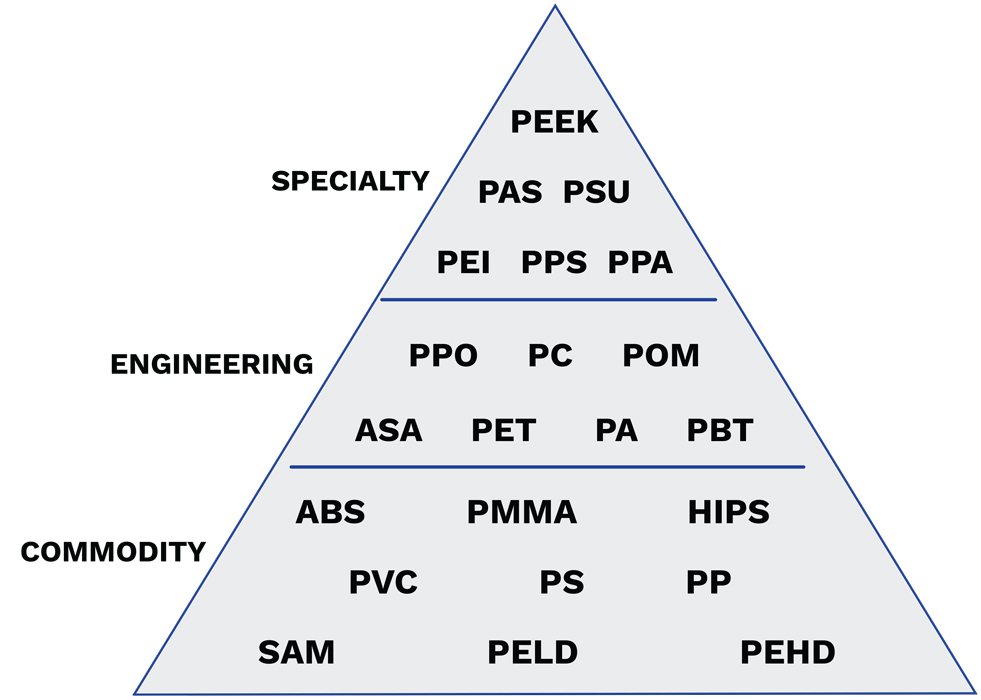
Once a polymer has been narrowed to a select family or group focus should be directed towards price and specific physical performance. Cost of materials should be compared in terms of cubic inch, not pound. Cost per pound can be misleading due to the density of a material doesn’t equate to the volume of the part. Physical characteristics can include tensile strength, izod impact, tensile elongation, flexural modulus, electrical resistance, hardness and many others. These characteristics will not be explained here, but are very useful to consider in polymer selection.