Five fundamental constituents make a cable: conductor, insulation, shield, filler, and strength member. The conductor carries the power or signal to its desired location. The insulation isolates the conductor from adjacent electrical paths. The shield protects the conductor signal integrity from RFI, EMI, and EMP sources. The filler is used to make the cable round by filling the voids of the imperfect wire packing. The strength member, when terminated properly, gives the cable a significant increase in axial strength. Extrusion geometry, material composition, weave pattern, plating, and various exotic operations can modify the cable to perform better in specific applications all having advantages and disadvantages that accompany it. Identifying a balance between these components and appropriate end-use is no easy feat and usually requires an experienced engineer to guide through the process.
Conductor
Starting with the design of the conductor; three main geometries exist: solid, stranded, and tinsel. The material composition of the conductor can be as exotic as the imagination, but some common examples are cadmium, phosphor bronze, chromium, steel, aluminum, platinum, silver, and of course copper. The most commonly selected conductor is copper due to its conductivity/cost factor. Silver has the highest electrical conductivity of all metals and it is also less susceptible to corrosion. Unfortunately silver costs more than copper and therefore is less commonly used as a homogenous conductor. Plating offers amore cost-effective solution to using precious metals. A copper cable can be plated with tin, gold, silver, or nickel to keep the advantages such as conductivity, corrosion resistance, and strength of particular precious metals. Other metals can be treated the same way, but copper is the most common candidate for plating.
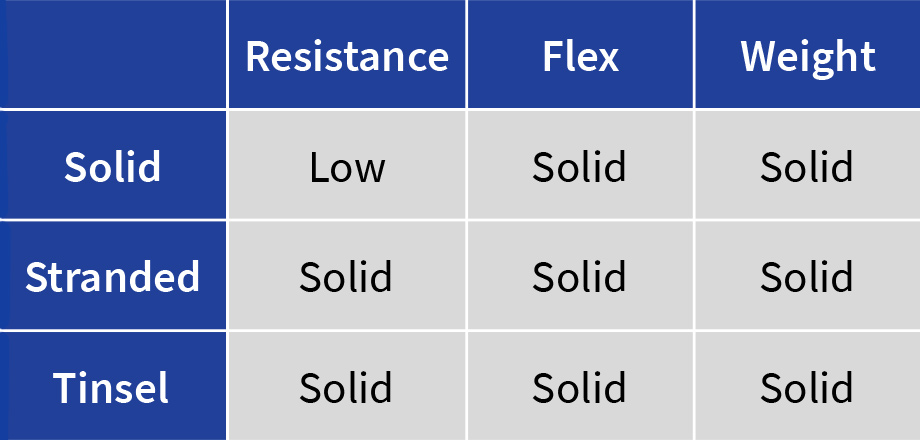
Primary Insulation
Primary insulation surrounds the conductor to protect signal integrity from adjacent electrical paths. Primary insulation can be made of various thicknesses depending on the allowable internal cable space and the required conductor isolation. Material composition may vary depending upon the environment it will be subject to and desired electrical characteristics.
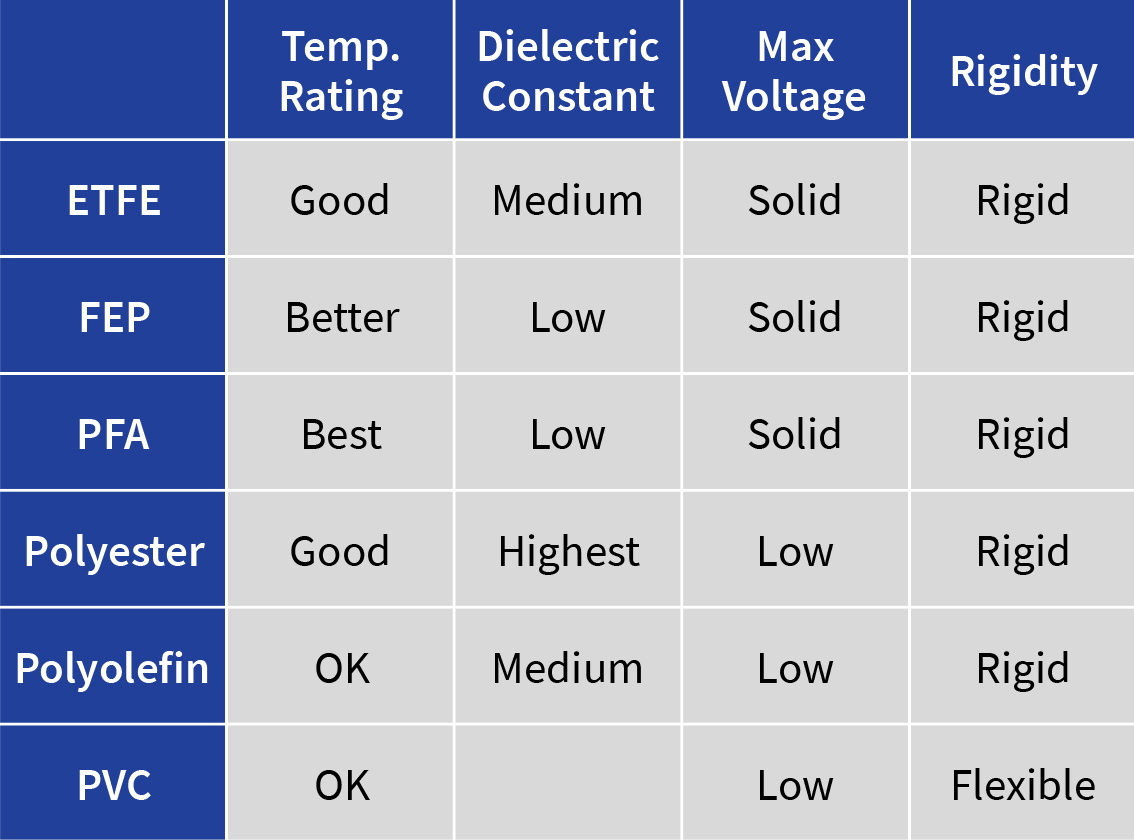
Jacket Insulation
Jacket insulations are usually limited to PVC, polyurethane, thermoplastic elastomer(TPE), silicone rubber, polyester, and fluoropolymers (PFA, FEP, and ETFE)depending upon the end-use application (See table under primary insulation for general polymer characteristics). Outer jacket insulations can be combined by twisting jackets together, molding a divider strip, or adding a zip jacket to combine them.
Shield
Three main types of shield weave patterns are braided, spiral, and foil. Materials commonly used are copper, tin-plated copper, silver-plated copper, nickel-plated copper, high and low-permeable irons, carbon fibers, tinsel wire, and aluminum. The characterization, like anything in this summary, depends upon the particulars, but below is a generalization of shielding characteristics.
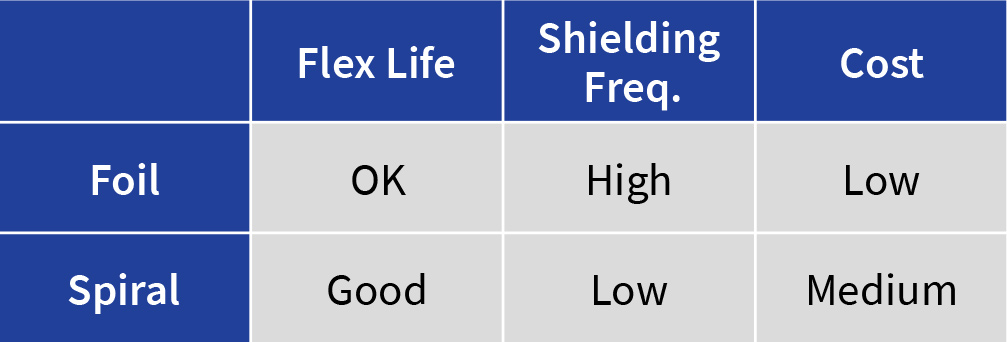
Filler & Strength Member
The filler material does as the name suggests, it fills the wire. Filler material can make the cross-sectional geometry in a desired shape, typically round. Strength members are included into cable construction when the conductor is subject to axial loads that it is unable to withstand. Tinsel wire is a common wire that usually requires strength members.
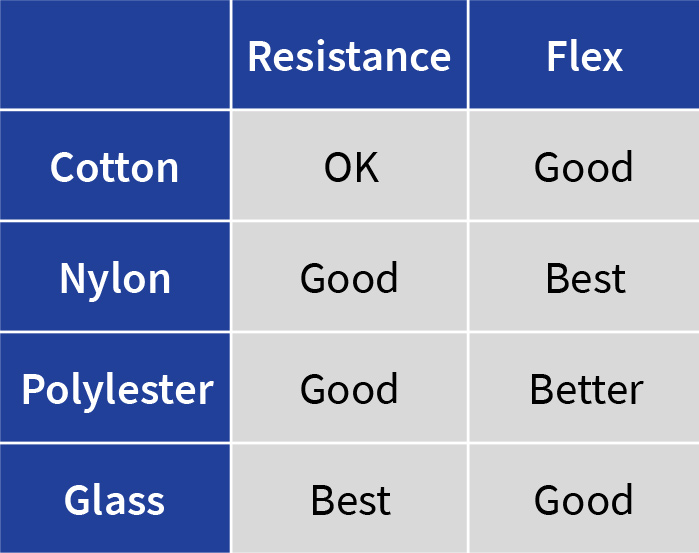